POLARIS has capabilities in optical fabrication for mirrrors of diameters up to 1200mm. Our mirrors are manufactured for applications in the near UV, the visible and the near IR. We polish mirrors in glass (fused silica, BK7…), ceramics (Zerodur…) or metal (aluminum, steel…).
The main technique we use for polishing mirrors is the technique of stressed-mirror polishing. This technique has been studied and developed at LAM since the 1960s. It consists in elastically deformaing (warping) the mirror during the polishing process in order to give it the opposite aspherical shape we want at the end. This approach permits to generate aspherization keeping the main advantages of a standard spherical polishing (good yield, continuity of the surface over the full clear aperture). With this approach, it is possible to manufacture highly-aspherized mirrors (off-axis parabola, hyperbola, toric mirrors and freeforms…) with very hig-quality optical surfaces in terms surface error (particularly for mid- and high-spatial frequency patterns classically generated by industrial robotic polishing with samll tools).
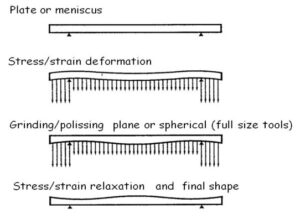
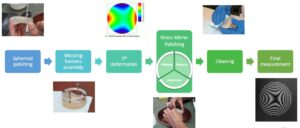
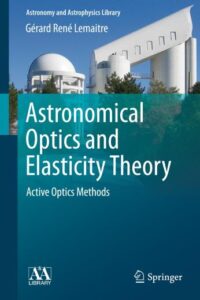